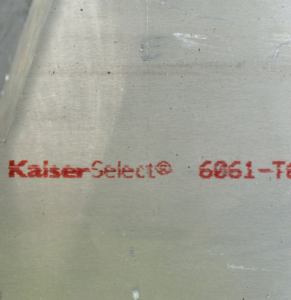
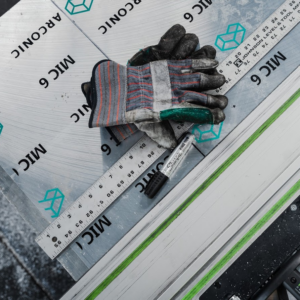
MIC-6 and 6061 are two of the most widely used aluminum alloys. MIC-6 aluminum is designed for dimensional stability, surface finish, and precision machining. 6061 aluminum is often selected for its versatility, weldability, and corrosion resistance. When you’re evaluating the pros and cons of using MIC-6 aluminum vs. 6061 aluminum for a component machining or a fabrication project, it’s useful to understand the properties, characteristics, and typical applications for each of these aluminum alloys.
MIC-6 Aluminum: Properties & Characteristics
MIC-6 aluminum was developed in response to the demand for aluminum plate requests to incorporate stability and tolerance improvements from what was on the market in the 1960s. Its continuous cast process is patented as it produces an aluminum alloy plate that is stable and immune to virtually all distortion during machining and temperature changes it may be subject to once it’s placed in use.
MIC-6 aluminum is preferred for machining applications that require precise control of tolerances and dimensions. It produces small uniform chips, even with high-speed machining operations, with minimal risk of plate distortion. MIC-6 is often the alloy of choice for manufacturing parts, components, and equipment used for precision measurement.
Tooling & Measurement | Component Manufacturing |
|
|
MIC-6 is weldable, but you’ll need to be extremely careful to avoid corrosion cracking. The MIG method is preferred to TIG as it minimizes the heat input. For more reliable weldability 6061 aluminum may be the best choice, depending on your needs.
6061 Aluminum: Properties & Characteristics
6061 aluminum is a precipitation-hardened alloy containing magnesium and silicon and is flat-rolled or extruded to produce, plate, bar stock, and round stock. 6061 aluminum is one of the most commonly-used heat-treatable aluminum alloys. Lightweight, strong, and corrosion-resistant even when the surface has been abraded, 6061 aluminum is very workable—easily cut, drilled, formed, tapped, and stamped, with excellent welding qualities. However, compared to MIC-6 aluminum, 6061 doesn’t lend itself as well to precision machining.
The weight-to-strength ratio, corrosion resistance, and weldability make 6061 aluminum the choice for a broad range of manufacturing and fabrication applications that require high-strength, corrosion resistance, and/or welding.
Aviation & Marine | Transportation |
|
|
Sporting Equipment | Manufacturing |
|
|
Top-Grade Aluminum for Every Purpose and Industry |
||
New Aluminum Plate 6061 |
New Aluminum Rectangular Bar |
All Aluminum Shapes |
![]() |
![]() |
![]() |
Customizable thickness: Measure in inches. You can get various options for all industry applications.
Can be cut to specific shapes and sizes: Excellent weldability to cater to unique project needs. Corrosion resistance: Grades like 6061-T651 are perfect for marine hardware applications that require superior rust resistance. |
Environmental resilience: Due to its heat treatable nature, 6061 aluminum does well in extreme conditions.
Wide selection of sizes and dimensions: Choose your sizes based on tensile strength, width, and weight. Good machinability: It’s lightweight and high strength makes it flexible for a number of applications. |
Reliable supply: Consistent, certified aluminum stock you can trust.
High-quality material: Superior-grade aluminum for precision needs. Custom cuts: Accurate cuts down to thousandths of an inch. |
Understanding the Differences: MIC-6 Aluminum vs. 6061 Aluminum
The table below provides a quick comparison of the major differences between MIC-6 aluminum and 6061 aluminum.
MIC-6 Aluminum | 6061 Aluminum | |
Production Method | continuous cast | flat-rolled or extruded |
Form | plate, bar | plate, bar stock, rounds |
Surface Finish | milled to 20 RMS or better | typically brushed to 60-90 RMS |
Corrosion Resistance | average | excellent |
Machinability | excellent | average |
Weldability | limited | excellent |
Best Uses or Applications | precision machining and instrumentation | structures and components where strength and corrosion resistance are required |
Where To Purchase Mic-6 Aluminum and 6061 Aluminum
Industrial Metal Service carries MIC-6 aluminum and 6061 aluminum sourced from Arconic and Kaiser, respectively. We also offer verified remnants of both of these alloys at a reduced price compared to new stock. Many machinists find that the remnant option is ideal for making prototypes or producing low-quantity production runs.