Molybdenum and tungsten are two refractory metals known for their extraordinary resistance to heat, making them invaluable in industrial applications. Both metals boast extremely high melting points relative to common metals, which contributes to their durability in high-temperature environments.
Their low thermal expansion coefficients provide exceptional material stability and facilitate close-tolerance machining, essential for ensuring optimal performance in precision components. Additionally, both molybdenum and tungsten offer excellent corrosion resistance, further extending their usefulness in various industrial sectors.
Despite the significant similarity when comparing molybdenum vs tungsten, a more detailed review of their differences and uses provides a better understanding of these heavy metals and their physical properties.
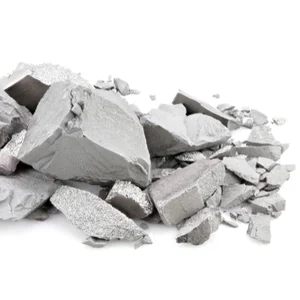
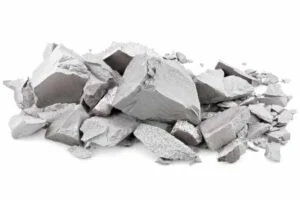
Tungsten: A Heavy Metal That Can Take the Heat
Tungsten is recognized for having the highest melting point of all metals, which makes it ideal for applications requiring materials that can withstand extremely high temperatures. This heavy metal is very dense and is often used in manufacturing applications where weight must be concentrated in small or constrained spaces, such as counterbalances in crankshafts.
Despite tungsten’s exceptional hardness, it remains extremely ductile, allowing it to be drawn into fine wires or ribbons used in electrical contacts, filaments in lighting, and various electronic components. Its low coefficient of thermal expansion, combined with its heat resistance, ensures minimal thermal expansion, which is crucial in maintaining the integrity of parts exposed to fluctuating temperatures.
Tungsten is also the material of choice for manufacturing high-temperature components in furnaces and heating elements. In addition, tungsten electrodes are essential in the Tungsten Inert Gas (TIG) welding process welding process, where their high melting point and refractory nature play a critical role.
Machining Tungsten Heavy Alloys
In most production applications, machine shops and fabricators typically use tungsten heavy alloys (WHA) because of their lower cost and superior machinability compared to pure tungsten. These alloys contain between 89% and 97% pure tungsten with the balance being nickel and copper or nickel and iron, depending on the alloy grade. The alloying elements improve machinability. Tungsten’s low thermal expansion allows very close machining tolerances for these alloys. WHAs are used in the manufacturing of aircraft counterbalances, ballast, racing weights, vibration reduction, radiation shielding, and military ordnance. One of the most-frequently-used WHAs is Densalloy.
Tungsten Densalloy
Tungsten Densalloy is 92.5% tungsten, 5.25% nickel, and 2.25% iron. This alloy is easily milled, turned, and drilled using carbide cutting and shaping tools. Coolant should be used for roughing and Densalloy can tolerate up to 1/8” depth cuts. For final finishing—up to .030”—coolant isn’t required. Densalloy can be cold worked by swaging.
One disadvantage of Densalloy is its poor weldability. And even though the alloy provides good corrosion resistance, if the end-use environment is extremely humid, consider finishing the component with nickel or cadmium plating, or acrylic or epoxy paints.
Molybdenum: Lower Melting Point and Density
Molybdenum, while also a refractory metal, has a lower melting point and density than tungsten, making it suitable for different industrial applications. Its high electrical conductivity, combined with low coefficients of thermal expansion and significant strength, makes it ideal for use in semiconductor base plates, industrial motors, aerospace components, and defense applications.
Molybdenum’s ability to improve the strength, electrical conductivity, and corrosion resistance of steel alloys is another crucial aspect of its industrial value.
Molybdenum is highly machinable, comparable to stainless steel when using certain techniques. It can be machined with conventional equipment, but cutting tools must be sharp to avoid edge breakage. Because molybdenum is abrasive, expect cutting tools to wear out more quickly compared to machining other metals like iron or steel. Similar to tungsten alloys, rough turning of molybdenum is acceptable with depths of cut up to 1/8″. For finishing work, a depth cut of 0.005” to 0.015” is recommended.
When welding molybdenum, it’s crucial to begin with a chemical cleaning to remove impurities. To achieve the best welding results, it is advisable to perform the process in a vacuum instead of an open atmosphere to prevent the material from absorbing nitrogen and oxygen, which can lead to oxidation and brittleness.
Buy Certified High-Quality Metals for Industrial Solutions |
||
New Aluminum |
New Steel |
New Stainless Steel |
![]() |
![]() |
![]() |
Reliable supply: Consistent, certified aluminum stock you can trust. High-quality material: Superior-grade aluminum for precision needs. Custom cuts: Accurate cuts down to thousandths of an inch. |
Durability and strength: Reliable for projects needing long-lasting, tough materials. Cost-effective: Quality steel that offers strength without breaking the bank. Custom cutting: Precise cuts tailored to exact needs with top-tier cutting tools. |
Sustainability: Highly eco-friendly as the most recyclable metal on earth. High durability: Resistant to corrosion and wear, ensuring long-lasting performance. Custom precision cuts: Tailored to your specifications with quick, accurate results. |
Molybdenum vs Tungsten: Cost-Efficient Sources
With such close similarities in their properties, whether or not to use tungsten alloys or molybdenum for a component is determined by design engineers, not machinists. Regardless of the choice of materials, either of these heavy metals can be machined without the need for special equipment or techniques.
One of the most significant challenges for many machine shops, however, is sourcing these metals at competitive prices.
Perhaps the greatest challenge for many machine shops is finding a reliable supplier who offers these metals at competitive prices. As an alternative to purchasing tungsten alloys or molybdenum sourced directly from the manufacturer, consider suppliers who specialize in verified remnants. In comparison to new materials, molybdenum and tungsten alloy remnants can be purchased at a lower price point. The best suppliers will work with you to closely match the remnant size to the dimensions of the parts you’ll be machining. With precision measurements, you’ll end up with less waste.
Whether for a long-term production run or a small order for a special project, purchasing verified tungsten or molybdenum remnants can often be the most economical approach to sourcing these heavy metals.