Ferrous metals are the unsung heroes that form the backbone of the modern world. These strong, versatile iron-based materials power everything from towering skyscrapers to smooth-sailing ships to the tiny components in your smartphone. The construction and manufacturing industries rely heavily on ferrous metals for their durability and reliability.
In this guide, we’ll dig into the nitty-gritty details of ferrous metals so you can understand what makes them tick. These ironclad MVPs have quite the story, from their characteristics, including magnetic properties and melting points, to their leading roles across today’s industries.
Read on to learn more about ferrous metals, their properties, and how they compare to non-ferrous metals.
What Are Ferrous Metals?
Simply put, ferrous metals are precious metals that contain iron content as their main element. They make up 90% of all refined metal production worldwide, thanks to iron being one of Earth’s most abundant metals. The “ferro” in their name comes from the Latin word for iron.
Along with an iron base, ferrous metals blend in carbon and other elements like chromium, nickel, and manganese to create super-strong alloys such as stainless steel, used in almost every industry. These alloys exhibit significant mechanical properties, such as high tensile strength and wear resistance, which make them indispensable in various applications.
So whenever you see sturdy structures like bridges built to last generations, those trusty cast iron cooking pots that never warp in your kitchen, or even the durable frame bolting your mattress together – you’ve got a ferrous metal to thank.
A Brief History on Ferrous Metals
Humans have utilized ferrous metals dating back over 5000 years to when early blacksmiths fashioned tools, jewelry, body armor, and weapons from meteorite iron. But it wasn’t until around 1200 BC that ancient steel-making allowed people to smelt iron ore into usable forms. This period marked the beginning of the Iron Age, a significant era that laid the foundation for modern ferrous material usage.
Fast forward a few millennia, and by the 19th century, ferrous metal production took off during the mass boom of railroads and skyscrapers. Innovations like the Bessemer process allowed bulk steel production, which fed rapid industrialization. This period saw the emergence of various steel alloys, each with distinct properties for specific uses.
When affordable Model T’s first rolled off Ford’s assembly lines in 1908, carbon steel parts enabled their construction and durability even at mass volumes. This introduction of low carbon steels revolutionized the automotive industry by offering a balance of strength and malleability.
Today, advanced alloys and computerized manufacturing allow for precise fabrication of everything from mammoth oil rigs to tiny nanotechnology. The evolution of alloy steels has brought about materials with enhanced corrosion resistance and higher tensile strength, essential for modern infrastructure.
The Most Common Ferrous Metals
The two most popular ferrous metals are iron and steel, but other types, including cast iron, wrought iron, and various steel alloys, also play crucial roles in construction and manufacturing industries.
Iron
As the base element of all ferrous metal products and the 4th most common element on Earth, iron comes out swinging with extreme durability. Structures from nearly 100% pure iron content boast unmatched strength and thickness.
This natural brute force makes pure iron a heavy-duty choice for applications like the following:
- Cast iron cooking pots that evenly distribute heat
- Wrought iron furniture that offers corrosion resistance
- Structural iron beams bearing immense weights
While iron withstands time and pressure, adding other metals to the mix enhances its properties even more, leading to the creation of alloy steels.
Steel
By blending iron with just a touch of carbon (2% or less), this iron-carbon alloy we call steel becomes lighter and more malleable than iron. Varying carbon content levels and additive metals like chromium, nickel, and manganese give different alloy steel types unique performance advantages. For example:
- Stainless steel resists rust and stains. Different types of stainless steel are labeled with an AISI three-digit number, e.g., AISI-2XX, AISI-3XX, etc.
- Structural steel bends without breaking
- Tool steel maintains shape at high temps
Indeed, mixing up steel’s metallic ingredients provides tailored solutions for countless applications. High carbon steels, with their superior hardness, are used in tools and machine parts, while medium carbon steels strike a balance between strength and ductility.
Beyond Iron & Steel
While iron and carbon steel make up most ferrous metals, other niche varieties like cast and wrought iron also make essential impacts.
Cast Iron
When iron ore is melted and cast into molds, this manufactures durable cast iron parts for heavy machinery, pipes, engines, and industrial uses requiring vibration damping. Cast iron’s low melting point makes it ideal for casting complex shapes, though it is less malleable than other ferrous metals.
Wrought Iron
Contrary to cast iron, wrought iron is heated and worked using tools to make different shapes and structures. Wrought iron consists primarily of iron with about 1-2% slag (a mixture of silicon, sulfur, phosphorus, and aluminum oxides). It is softer and more tensile than cast iron, making it suitable for decorative work and structural components where ductility is crucial.
Alloy Steels
By adding metals like chromium, titanium, and silicon to carbon steel, specially formulated alloy steels gain properties like heat resistance, wear resistance, and extra hardness for use in everything from bridges to surgical tools. These other alloying elements can significantly impact the mechanical properties, enhancing the material’s performance in demanding environments.
Buy Certified High-Quality Metals for Industrial Solutions | ||
New Aluminum | New Steel | New Stainless Steel |
![]() | ![]() | ![]() |
Reliable supply: Consistent, certified aluminum stock you can trust. High-quality material: Superior-grade aluminum for precision needs. Custom cuts: Accurate cuts down to thousandths of an inch. | Durability and strength: Reliable for projects needing long-lasting, tough materials. Cost-effective: Quality steel that offers strength without breaking the bank. Custom cutting: Precise cuts tailored to exact needs with top-tier cutting tools. | Sustainability: Highly eco-friendly as the most recyclable metal on earth. High durability: Resistant to corrosion and wear, ensuring long-lasting performance. Custom precision cuts: Tailored to your specifications with quick, accurate results. |
How Ferrous Metals are Produced
We couldn’t enjoy the versatile applications of ferrous metals without miners sourcing the raw ferrous materials and massive foundries churning out refined alloys like alloy steel and more. The following is a look at how iron gets converted into steel:
- Iron ore containing hematite and magnetite gets mined from underground mines or rocky open pits. While Australia and China lead global iron production, the U.S., Canada, and India also mine substantial amounts.
- In blast furnaces, coke (processed coal) purifies iron ore into liquid pig iron, which contains around 92%–94% iron content—layers of iron ore, coke, and limestone heat to nearly 3000°F to enable this reduction reaction.
- Bessemer converters or basic oxygen furnaces mix liquid pig iron with precise amounts of air or pure oxygen to lower carbon levels and produce crude steel.
- Alloying elements are added to molten steel batches to create desired grades used for automotive, structural, or stainless steel. Electric arc furnaces directly melt recycled steel scrap to manufacture new steel.
- Continuous casting turns cooled steel into preliminary slab, bloom, or billet shapes easily reheated and rolled into final parts later, like I-beams, tools, or appliances, depending on the application.
Ferrous Metals Properties and Characteristics
Ferrous metals exhibit unique properties that define their identity and value across industries. These include the following:
- Magnetic properties in terms of attraction due to iron’s atomic structure
- Mechanical properties, namely high hardness and tensile strength from carbon blending
- Durability and wear resistance promoting long service life
- Excellent thermal and electrical conductivity transfer (except stainless steel)
This combination of beneficial qualities makes ferrous metals MVPs of manufacturing and structural integrity. The properties of ferrous metals, such as ductility and corrosion resistance, ensure their widespread use in many construction materials and tools.
Main Applications and Uses of Ferrous Metals
With great tensile strengths come great applications. Here are the practical applications of ferrous metal.
1. Construction & Infrastructure
From soaring city skylines to smooth highway expansions, ferrous metals form the strong skeletal frames holding civilizations together. Steel gives us the following:
- Concrete reinforcement
- Structural support beams
- Resilient building frames
2. Transportation
As you drive or fly to your destination, you have ferrous metals to thank for getting you there swiftly and safely. Iron and steel make transportation possible by allowing us to create the following:
- Vehicle bodies and engines
- Aircraft frames and components
- Railroad tracks and cargo containers
3. Energy
Drilling for pipelines or fossil fuels depends on hardy ferrous metals that can take the heat. They allow the construction of the following:
- Offshore oil rigs and platforms
- Gas pipeline transmission
- Steam and hydroelectric turbines
4. Appliances and Electronics
Even creating smaller gadgets and goods that enhance domestic life involves hardy ferrous metals. Applications include the following:
- Internal frames, coils, and motors
- Computer cases and internal parts
- Microwave and dishwasher cavities
Advantages and Disadvantages of Ferrous Metals
Here are the pros and cons of ferrous metals.
Pros
- Durability and Tensile Strength: The ironclad toughness of ferrous metals ensures products and structures built with them go the distance through rugged reliability and resilience, matching industry demands.
- Availability and Affordability:With iron ore and coal abundantly available worldwide, ferrous metal production scales massively to meet consumption needs across societies. Their economy of scale makes ferrous metals affordable options.
- Recyclability.Unlike plastics and wood rotting away in landfills, ferrous metals are continually recycled and reconstituted without losing their durability. Their closed-loop lifecycle scores sustainability points.
Cons
- Weight: Pure iron and carbon steel have much higher densities than alternative metals like aluminum, which means heavier products and costlier shipping.
- Corrosion Resistance: Exposed steel corrodes with environmental contact over time through oxidation and rust accumulation unless properly galvanized or stainless steel is used.
- Embrittlement: Steel can lose adaptability over time and repeated stress, becoming rigid and brittle unless precautions are taken during manufacturing processes.
Ferrous Metals Recycling and Sustainability
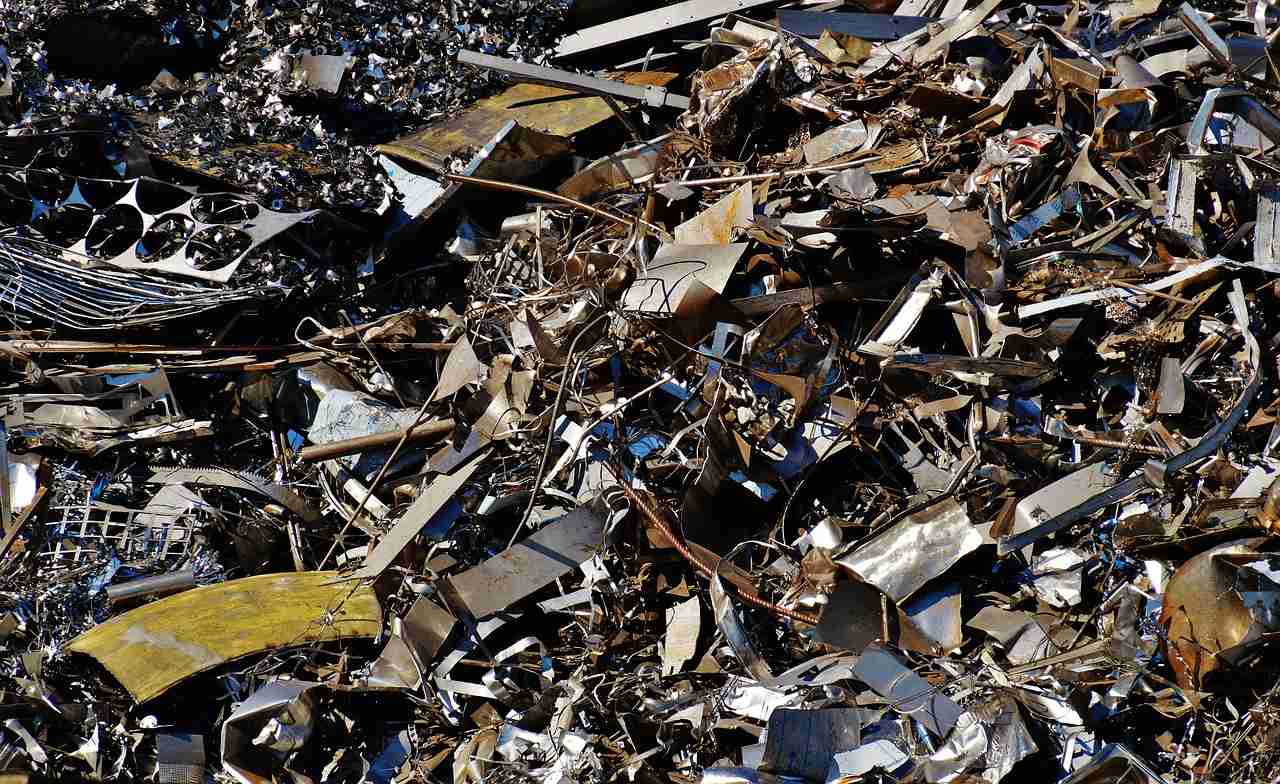
One shining advantage ferrous metals boast is a responsible environmental footprint through recycling. Around 70% of all steel and iron gets recycled – more than paper, plastic, and aluminum combined.
Rather than corroding in landfills, recovered ferrous metals from junked cars to demolished buildings get quickly remelted in electric arc furnaces, skipping the mining and refining steps. This circular life cycle skips half the carbon emissions and energy demands of virgin production.
How Ferrous Metals Compare to Non-Ferrous Metals
While ferrous metals dominate construction industry applications, they have another family of metals providing alternatives—non-ferrous metals. Many non-ferrous metals, such as aluminum and copper, offer lower densities and superior electrical conductivity, making them essential in different contexts.
Let’s compare some core differences between these two.
Property | Ferrous Metals (Average Values) | Non-Ferrous Metals (Average Values) |
Density (g/cm³) | 7.8 (for steel) | 2.7 (for aluminum), 8.96 (for copper) |
Melting Point (°C) | 1,370 (for steel) | 660 (for aluminum), 1,085 (for copper) |
Electrical Conductivity (% IACS) | 3%–15% (for steel) | 61% (for aluminum), 100% (for copper) |
Tensile Strength (MPa) | 400–550 (for steel) | 70-500 (for aluminum), 210-500 (for copper) |
Thermal Conductivity (W/mK) | 50–58 (for steel) | 237 (for aluminum), 401 (for copper) |
Young’s Modulus (GPa) | 200 (for steel) | 70 (for aluminum), 110 (for copper) |
The table above provides average values for some common ferrous and non-ferrous metals (steel, aluminum, and copper). It’s important to note that these values can vary significantly depending on the specific alloy and treatment of the metal. The difference between ferrous and non-ferrous metals is crucial when selecting materials for specific applications.
Bottom Line
From ancient blacksmiths pounding meteoric iron into weapons to today’s regenerative steel mills powering more sustainable societies, ferrous metal products undergird human advancement through their unparalleled usefulness, balancing strength, value, and abundance.
Yet as wondrous as ferrous alloys continue empowering modern life, they also face production and emissions challenges requiring cleaner breakthroughs as populations grow. Thankfully, increasing recycling loops plus emerging hydrogen and electrical steel-making methods can help decarbonize ferrous metal life cycles to sustain this vital industrial resource for future generations.
So next time you grab a stainless steel-framed shovel, ride an iron-fortified elevator, or watch a bridge’s crisscrossed steel supports race by outside your train window, take a second to appreciate all the fused science, sweat, and visionary spirit embedded in those resilient, ferrous metal structures.
Our comfortable lifestyles depend on them more than ever.