Why do some metal parts outlast others in the toughest conditions? The secret lies in case hardening—a technique that boosts outer surface durability while maintaining internal toughness.
The blend of surface hardness and core ductility makes case hardening indispensable across many industries, from automotive to aerospace. It’s a crucial process for parts that endure constant friction and impact, such as gears and camshafts.
This article unpacks the importance of case hardening, shedding light on its role in enhancing the performance and longevity of critical machinery components.
What Is Case Hardening?
Case hardening is a specialized metallurgical technique that enhances the surface hardness of metal parts, creating a hard, wear-resistant layer while preserving a softer, more flexible core. This process ingeniously merges the advantages of soft and hard metals into a single component.
The softer core of a metal part is excellent at absorbing impacts and resisting fracture. However, this softer material lacks the necessary resistance to wear and tear. Case hardening addresses this by hardening only the exterior, dramatically improving abrasion resistance without sacrificing the core’s beneficial properties.
Case hardening typically involves heating the metal to high temperatures. This process alters the metal’s surface, creating a hardened, thin layer that significantly extends the component’s lifespan by reducing surface wear.
Historical Fact: Case hardening traces back to the Iron Age, when carbon sources like bone or charcoal were used to harden iron weapons. |
Types of Case Hardening Processes
Case hardening is not a one-size-fits-all procedure but a category of several techniques, each with its unique applications, advantages, and mechanisms. These methods allow for the customization of the hardening process to suit the specific requirements of different metals and their intended uses.
Carburizing
Carburizing enriches the surface layer of steel with carbon at high temperatures. This method is ideal for low-carbon steel, significantly improving its surface toughness and wear resistance. The process involves a heat treatment process for the metal in a carbon-rich environment, allowing carbon to diffuse into the surface, and is often followed by quenching to lock in the hardness.
Nitriding
Nitriding introduces nitrogen to the steel surface. It’s performed at lower temperatures compared to carburizing and does not require quenching. This creates a highly wear-resistant thin layer with the added benefit of minimal distortion, making it suitable for alloy steels.
Cyaniding
A rapid process, cyaniding immerses steel tools or parts in a molten cyanide bath to introduce both carbon and nitrogen to the surface. While it’s fast and effective for small parts, the use of cyanide poses health and environmental risks, limiting its widespread use.
Carbonitriding
Carbonitriding adds both carbon and nitrogen to the steel’s surface at lower temperatures. This process is particularly useful for parts that might distort at the higher temperatures used in traditional carburizing. It enhances hardness and wear resistance in both low carbon and alloy steels, which makes it a versatile choice for a wide range of applications.
Buy Certified High-Quality Metals for Industrial Solutions | ||
New Aluminum | New Steel | New Stainless Steel |
![]() | ![]() | ![]() |
Reliable supply: Consistent, certified aluminum stock you can trust. High-quality material: Superior-grade aluminum for precision needs. Custom cuts: Accurate cuts down to thousandths of an inch. | Durability and strength: Reliable for projects needing long-lasting, tough materials. Cost-effective: Quality steel that offers strength without breaking the bank. Custom cutting: Precise cuts tailored to exact needs with top-tier cutting tools. | Sustainability: Highly eco-friendly as the most recyclable metal on earth. High durability: Resistant to corrosion and wear, ensuring long-lasting performance. Custom precision cuts: Tailored to your specifications with quick, accurate results. |
Advantages of Case Hardening
The following benefits underscore why a case-hardened metal is the preferred choice for enhancing the durability and performance of components.
Wear Resistance
When components are subjected to harsh environments or high-friction applications, wear and tear can quickly become a concern. Case hardening creates a robust outer layer that can withstand the rigors of constant use. Gears, bearings, and other mechanical parts treated with case hardening exhibit remarkable resistance to abrasion.
Surface Hardness
The key advantage of case hardening lies in its ability to impart a wear-resistant and hardened surface layer while maintaining a ductile core. This unique combination provides components with exceptional resistance to indentation and scratching. Whether it’s heavy machinery operating in rugged terrain or precision tools subjected to intense pressure, surface hardening offers unparalleled protection.
Enhanced Fatigue Strength
In applications where components undergo repeated stress cycles, fatigue failure can pose a significant risk. Case hardening mitigates this risk by improving the fatigue strength of the material. By creating a tougher surface layer, the process reduces the likelihood of cracks and fractures.
Corrosion Resistance
Beyond mechanical wear, corrosion represents another formidable challenge for metal components exposed to harsh environments. Case hardening can play a vital role in enhancing a material’s resistance to corrosion. The hardened layer acts as a shield against moisture, chemicals, and other corrosive agents. This reduces the need for frequent replacements and repairs.
Dimensional Stability
Unlike some heat treatment methods that can induce distortion or warping, case hardening minimizes these effects, ensuring that components retain their precise dimensions. This level of accuracy is critical in industries where tight tolerances are essential for proper functioning and assembly, such as automotive manufacturing and aerospace engineering.
Cost-Effectiveness
By selectively hardening only the surface layer of a component, manufacturers can utilize lower-cost, lower-alloy materials for the core without sacrificing performance. This optimization not only reduces material costs but also streamlines production processes, resulting in significant savings over time.
Efficiency Insight: Leveraging advanced simulation software in case hardening processes can optimize heat treatment cycles, reducing energy consumption and further cutting production costs. |
Suitable Materials for Case Hardening Processes
Choosing the right material is crucial to achieving the desired balance of core and surface hardening. Each material reacts differently to the introduction of carbon, nitrogen, and other elements, influencing the final properties of the component.
The table below provides a comparison of commonly used materials in case hardening and their compatibility with various hardening processes.
Material Type | Carburizing | Nitriding | Cyaniding | Carbonitriding |
Low Carbon Steel | Yes | No | Yes | Yes |
Alloy Steel | Yes | Yes | No | Yes |
Cast Iron | Limited | Yes | No | Limited |
Stainless Steel | No | Yes | No | Yes |
Applications of Case Hardening
Case hardening is a versatile process used across various industries to enhance the durability and lifespan of metal components. Let’s explore its wide-ranging impact on modern manufacturing and engineering.
Automotive Industry
- Gears and shafts: Increases wear resistance, essential for transmission components.
- Bearings: Improves surface toughness, which is crucial for reducing friction and extending lifespan.
Aerospace Industry
- Landing gear components: Enhances strength and fatigue resistance for enhanced safety and reliability.
- Turbine components: Boosts surface durability to withstand high temperatures and stresses.
Firearms and Defense
- Bolt carrier groups: Ensures durability under rapid firing conditions.
- Barrel interior: Hardens surfaces to resist wear from high-velocity projectiles.
Machinery and Tooling
- Cutting tools: Extends tool life by improving wear resistance.
- Dies and molds: Increases surface hardness, essential for shaping other materials.
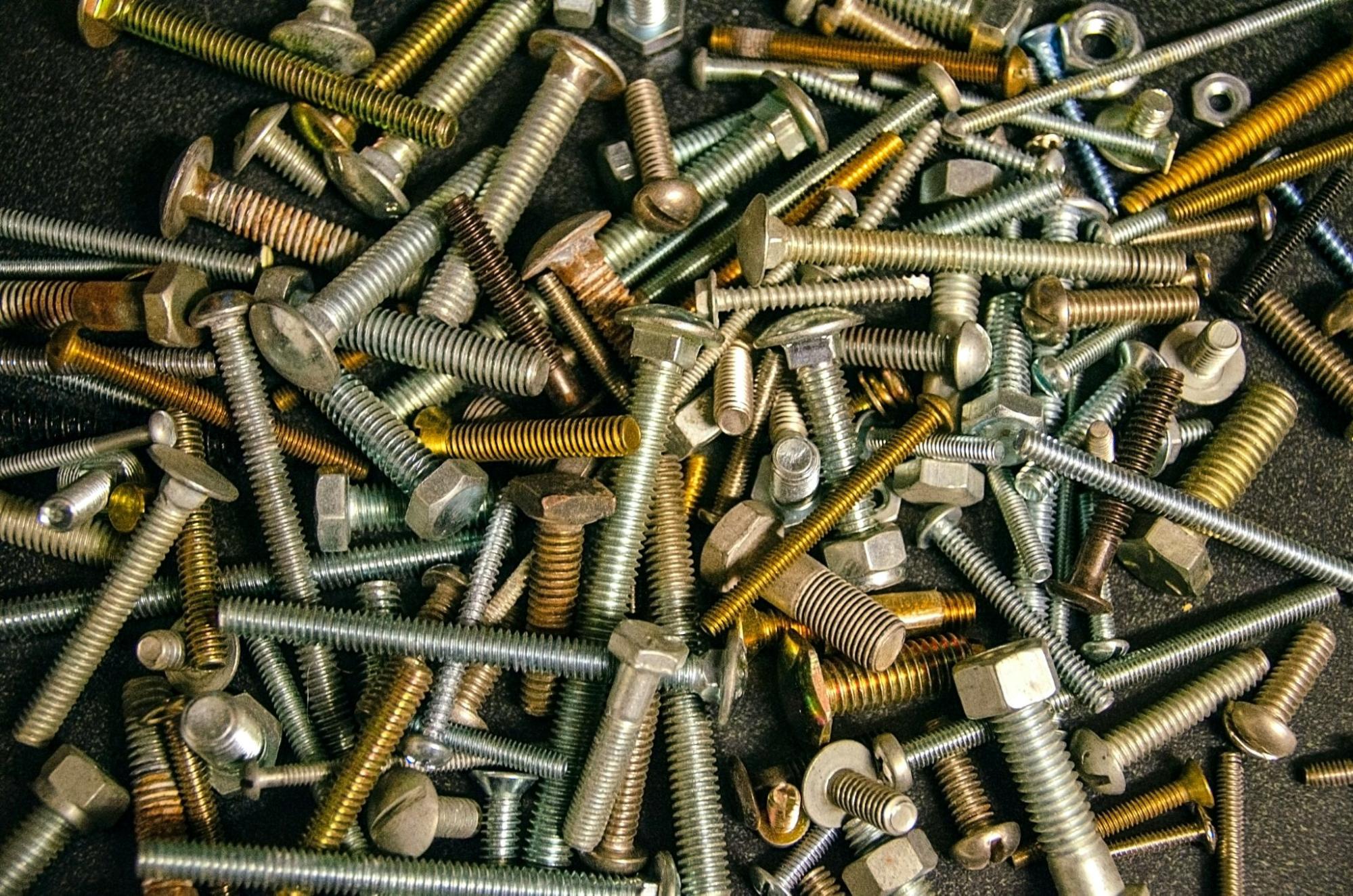
Case Hardening Parameters
The effectiveness of case hardening depends on various process parameters that must be carefully controlled to achieve the desired surface toughness and core properties. The following are the key parameters involved in case hardening and their impact on the final component properties.
Temperature
The temperature at which the case hardening process is conducted plays a critical role in determining the depth of the hardened layer and the diffusion of hardening elements into the material. Higher temperatures accelerate the diffusion process but may also increase the risk of distortion and grain growth. Conversely, lower temperatures may result in insufficient hardening depth.
Time
The duration of the process, often referred to as the “soaking time,” influences the depth of hardening and the diffusion of hardening elements. Longer soaking times allow for greater penetration of hardening elements into the material, resulting in a deeper hardened layer. However, excessive soaking times can lead to grain coarsening and surface decarburization.
Hardening Medium
Various hardening mediums, such as gas, liquid, or solid compounds, can be used in the case hardening process. Each medium offers distinct advantages and limitations in terms of process control, uniformity of hardening, and environmental considerations. The selection of the appropriate hardening medium depends on factors such as material type, component geometry, and desired hardening depth.
Eco Tip: Switching to low-emission hardening mediums, like water-based solutions or natural gas, offers a cleaner alternative that aligns with sustainability goals in case hardening processes. |
Quenching Method
Quenching is a critical step where the heated component is rapidly cooled to room temperature to achieve the desired hardness. The choice of quenching method, whether it be oil, water, or air quenching, influences the rate of cooling and the resulting microstructure of the material. Proper quenching is essential to minimize distortion, cracking, and residual stresses in the hardened component.
Surface Preparation
Surface preparation, including cleaning and surface roughening, is essential to ensure uniform diffusion of hardening elements and promote adhesion of the surface layer. Proper cleaning removes contaminants and oxide layers from the surface, while surface roughening enhances the surface area for effective diffusion. Careful attention to surface preparation can improve the consistency and quality of the hardened layer.
Post-Hardening Treatments
After the case hardening process, certain post-hardening treatments may be performed to enhance the properties of the hardened component further. These treatments may include tempering, stress relieving, or surface finishing operations to improve dimensional stability, reduce residual stresses, or achieve specific surface characteristics.
Frequently Asked Questions
Here are some of the most common questions about this process to give you a deeper understanding of how it works.
How does diffusing carbon into the outer surface improve a part?
Diffusing carbon into the outer surface of carbon steel parts increases their surface hardness significantly. This hardened layer is more resistant to wear and tear, extending the lifespan of the part. It’s particularly useful for low-carbon steel parts that need extra durability for demanding applications.
What is the critical temperature in case hardening?
The critical temperature in case hardening is the specific temperature range to which steel must be heated before diffusing carbon. Heating to this temperature allows the carbon atoms to penetrate the outer surface of the steel, initiating the hardening process.
How do flame hardening and induction hardening differ?
Flame hardening applies direct heat to the steel’s surface using a high-temperature flame, reaching the critical temperature for diffusing carbon. Induction hardening uses electromagnetic induction to heat the steel uniformly, providing precise control over the hardening process. Both methods are effective, but the choice depends on the specific requirements of the steel components being treated.
Why is case-hardened steel preferred for certain applications?
Case-hardened steel is preferred for applications where high wear resistance and durability are critical. The process of case hardening creates a tough, wear-resistant outer layer on steel components, making them ideal for use in environments where they are subjected to heavy loads, high friction, or impact. This makes case-hardened steel parts essential in industries like automotive, aerospace, and manufacturing.
Can all steel components be case-hardened?
Not all steel components are suitable for case hardening. The process is most effective on low-carbon steel parts, where the addition of a hardened outer surface can significantly improve wear resistance and strength. High carbon steels or other types of metals may require different treatment processes to achieve similar results.
Conclusion
The versatility and effectiveness of case hardening make it a cornerstone of metallurgy. From automotive transmission components to aerospace turbine parts, its benefits are felt far and wide, enhancing the performance and safety of critical machinery.
As a linchpin of modern manufacturing, case hardening continues to drive innovation and empower machinery to excel under the toughest conditions.